|
|
|
Testing
|
Rise Profile |
Reaction
Temperature |
Pressure Measurement
|
Viscosity
|
Curing Monitor
Device | Advanced
Test Container |
Box Foam Setup
|
Balance Integration
| System Configuration |
|
Foam Qualification System
FOAMAT®
Measuring Physical Parameters During Foam Formation
|
|
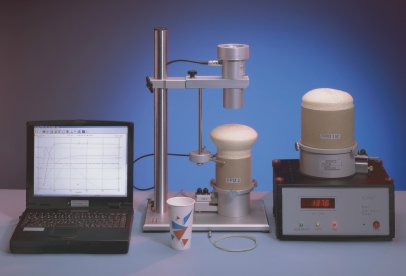
Fig. 1. The foam qualification system FOAMAT with the ultrasonic fan sensor
PFT, a thermocouple, and the pressuremeasurement devices FPM 2 and FPM 150. The
measurement sequence and the data processing are controlled by the software ,,FOAM”
(left).
* covered by several
patents
|
Simultaneous measurement of foam
rise height, reaction temperature, rise pressure, curing, weight loss and
viscosity
Master curves for quality
assurance testing in production control (ISO 9001)
Easy to use Windows based FOAM
software
High performance sensors for all
foam, types
|
|
Foam Testing
The quality of polyurethane (PU) foams depends on what happens
during their formation. It therefore makes sense to record the formation
parameters by suitable means and to check these regularly on representative
samples. Consistent product quality is ensured by measuring the formation
parameters of samples of starting materials prior to the actual foaming process
and to compare them with specified standards in the form of master curves. Many
automotive systems suppliers apply this method to vehicle-interior parts and
modules. The furniture industry, along with the equipment insulation and
construction industries, also measures formation parameters for the purposes of
quality assurance. When foam systems with special properties are being
developed, measuring the formation parameters gives an insight into how the
reaction is proceeding and how foam formation can be affected by additives,
blowing agents, stabilizers and the mixing ratio. The Foam Qualification System
FOAMAT® meets both stringent requirements on measuring accuracy and versatility
in accommodating different sample containers.
top |
|
Rise Height and Rise Profile
Measurement
The
classic method for characterizing
foams
is to determine the
rise
height or rise profile by measuring
the
change in height due to
the
expansion of the foam
sample
in a
cup, a cardboard box or a
cylindrical container. The start
time is generally accepted to be
the
start of the reaction between
the mixed components A
(polyol + additives) and B (isocyanate)
after
mixing. The rise
time
is the time which elapses
until maximum
expansion has
occurred. The patented ultrasonic
fan sensor PFT of the FOAMAT®
system
(Figs. 1,
2)
can
be used
for
all types
of
foams, including rigid foams
with
large heat release. The rise
profile is the fingerprint of a foam.
During
quality assurance testing,
it is
compared with given master
curves. A master curve (Fig.
3)
is
a
tolerance band showing the
margins of the rise profile for a
“good”
foam sample. Rise height
measurement is still the standard
test
in foam qualification.
With
the FOAMAT® system new
measurement techniques have
become available, revealing more
detailed information of the foam
generation process.
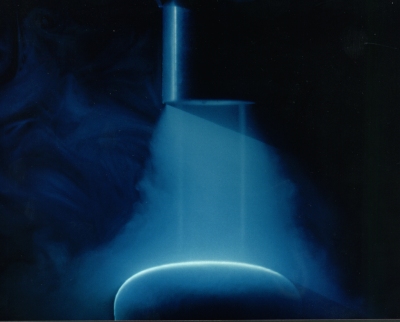
Fig. 2. The
patented ultrasonic fan sensor PFT ventilates the surface of the
rising foam.
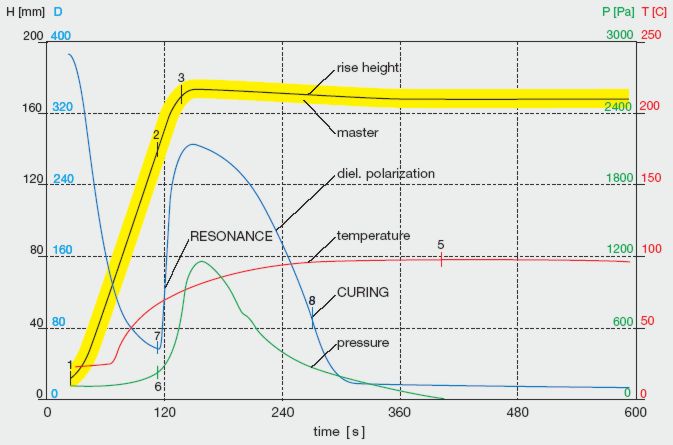
Fig. 3. The
experimental data for rise height, temperature, rise pressure,
dielectric polarization, and loss of mass are recorded simultaneously
by the software FOAM and are displayed in a graph. The figure shows
the curves for a semi rigid foam measured with FOAMAT and FPM/CMD2.
top |
|
Reaction Temperature
The
exothermal cross linking
reaction causes the temperature
increase in the foam sample. Thin
thermocouples are ideal for
measuring the temperature inside
the
foam because they have a
low heat capacity and are easy to
handle. They interfere little with
the
foam formation and can be
used
repeatedly.
top |
|
Foam
Pressure
Measurement
Pressure builds up in the foam
after
the components have set.
Stable cell walls are formed that
prevent the foam from expanding
further and to release blowing
agents. Thus, wall elements, panels
or
sheet metal are stressed at
right
angles to the direction of
foam flow if they are foam
backed
for
the purpose of providing
insulation or rigidity. As high
pressure forces are generated,
the
production equipment has to
be
reinforced or supported. The
forces are measured as the rise
pressure, so called because the
local stress present inside the
foam after setting is critically
dependent on the foam rise
height. The rise pressure is measured
with
the patented FPM
(Foam
Pressure Measurement)
device. The FPM replaces
usual
test cups.
Whereas the rise curve reflects
the
dynamics of blowing agent
generation, the rise pressure mirrors
the
cell properties, which are
affected by the polymerization
reaction. Measuring the pressure
can
yield important information
about
the effects of catalysts and
stabilizers on the setting reaction.
For
production purposes, the
pressure curve determines the gel
point
and the pressure decay,
which
indicates when to open the
mould.
Since the foam is free to
expand
upwardly while the pressure
is
being measured, the ultrasonic
fan
sensor PFT can
measure the rise height simultaneously.
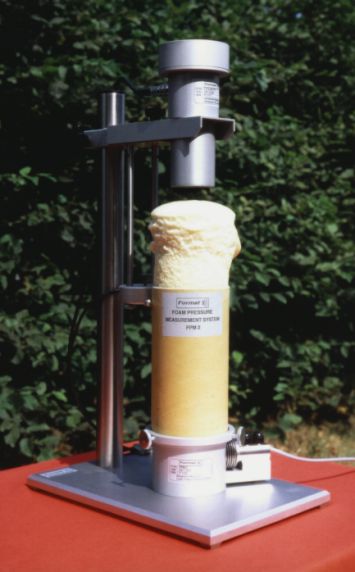
Fig. 4.
FPM 2 on the stand of the
Foam Qualification System FOAMAT®.
top
|
|
Viscosity
Determination
A particular advantage of measuring the pressure
by the
FPM
is that it allows the viscosity of the foam to be calculated directly
from the experimental data provided by FOAMAT®. This is
achieved by using the Hagen-Poisseuille viscosity model. The model
starts on the assumption that the viscosity is determined by the force
necessary to move a longitudinal element of foam at a specified speed
through a tube, which is the
FPM
in this case. The reaction force is obtained directly from the rise
pressure. The pressure data and the rise height curve measured in the
FPM
are sufficient for calculating the viscosity vs. time. For producers,
the viscosity gives additional information for optimizing the process
control in moulded foam production.
top |
|
Dielectric Polarization
Measurement
Dielectric polarization is a new
measurement parameter that
gives
insight into the electrochemical
processes occurring during
foam formation. Dielectric
polarization is essentially determined
by
chain-like molecules
with a
large dipole moment due to
their polar ends (OH, NCO). Chain
formation precedes the crosslinking
reaction that ultimately
suppresses all dipole mobility during
curing. The dielectric polarization
sensor
CMD (Curing Monitor
Device)
is located in the bottom
section of the FPM (Fig.
5).
The dielectric polarization shows the formation of intermediates
like
polyurea and displays
the
final curing of the foam
giving
a constant signal after the
chemical reaction is completed.
CMD
is
provided in combination
with
the pressure measurement
device FPM. In order to simulate
the production conditions in a
mould,
the CMD sensor can be
heated
with closed loop control.
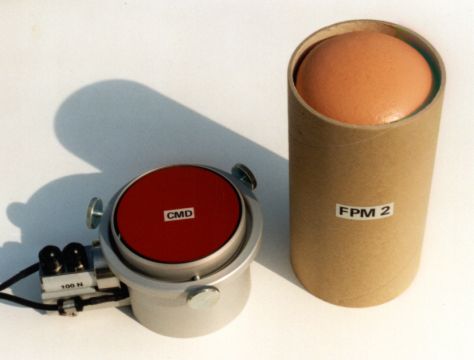
Fig. 5. The
polarization sensor CMD which is integrated into the FPM device
measures the dielectric polarization of a foam sample simultaneously
with the rise pressure. Right: the foam specimen in the removed
cardboard cylinder.
top |
Advanced Test
Container ATC
Undefined
test container temperatures spoil the correlation between the test
result and the production situation. PIR foams require external heat
to react and cure properly. Otherwise these formulations remain sticky
and voids appear. To overcome this, Format Messtechnik GmbH has
introduced the temperature controlled Advanced Test Container ATC
(Fig.
6). Another advantage of the new precise temperature controlled
test container is the better reproducibility of the measurement data
compared to non temperature controlled systems.
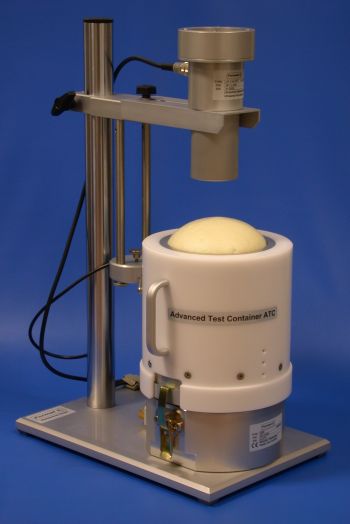
Fig. 6. The Advanced Test
Container ATC is a temperature controlled test container giving most
reproducible and production near test results.
top |
Extra Large Advanced Test
Container ATC XL
For testing
bigger foam quantities under temperature controlled conditions, Format Messtechnik GmbH has
introduced the extra large temperature controlled Advanced Test Container ATC
XL
(Fig.
7). The ATC XL has four times the test volume of the standard
ATC. They both comprise an upper and a lower part, which are clamped
by spring locks. The foam sample can easily be recovered through the
bottom opening. An additional release mechanism is available.
Fig. 7. The Advanced Test Container ATC XL is placed on the stand
of the Foam Qualification System FOAMAT®. The ATC XL has four times
the test volume of the standard ATC.
top |
Box Foam Setup
The Box Foam Setup comprises the Box Foam
Container BFC 200, the extended mechanical set and a metal
sheated thermocouple. The Box Foam Setup is specially designed to
measure the rise height and the core temperature of slabstock foam
samples. The BFC 200 is made of Pertinax walls forming a cube with an
edge length of 200mm. For easy access to the finished foam sample two
of the walls are hinged and can be flapped aside. A thermocouple
holder is mounted at the upper edge of the BFC 200. It has a boring at
an angle of approximately 45 degrees for inserting a thermocouple into
the center of the foam. The extended mechanical set is larger than the
standard mechanical set and is equipped with a second cup receptacle,
turned to the right hand side of the stand.
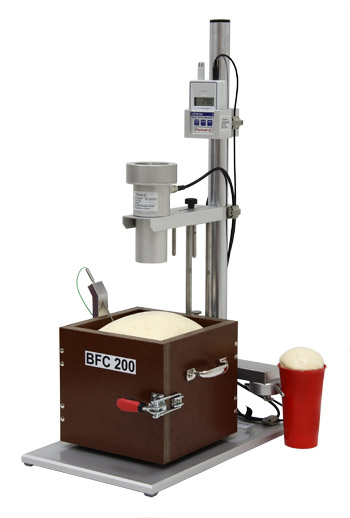
Fig. 8.
The
BFC 200 is placed onto the base plate of the extended mechanical set.
The thermocouple is inserted into the
center of the foam.
top |
Balance
Integration
To
obtain reproducible experimental
data,
the reaction components
must be weighed out exactly.
Despite the utmost care on the
part of the user remnants adhering
to the
mixer head and remaining in
the mixing cup lead to differences
in the
tested foam mass.
Integrating a laboratory balance
into the FOAMAT® system (Fig.
9)
provides automatically recording
the
mass of each component in
the
batch documentation.
Additionally, loss of mass due
to the
release of blowing agents
and
volatile components during
foaming can be recorded continually.
Determining the foam density
from the mass of the finished
foam
sample and its final height is
another advantage of an integrated
balance.
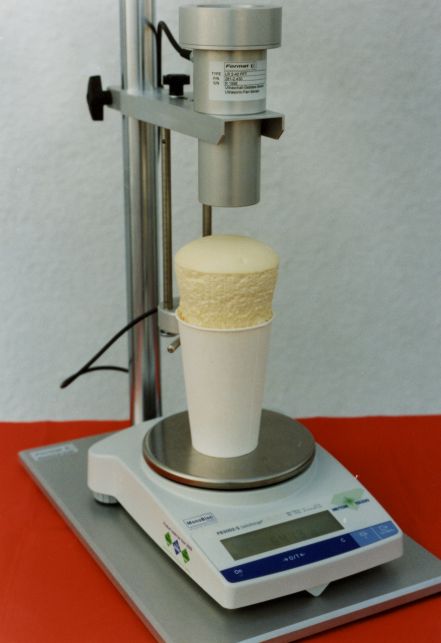
Fig. 9. For measuring
the loss of mass, the test cup is placed on a laboratory balance with serial
data interface.
top |
|
System Configuration
The
complete Foam Qualification
System FOAMAT® and its periphery
is
shown in Fig.
10.
The mixer
operation is controlled by the software
FOAM
according to the
user’s input. The controller unit and the balance
are
connected to the PC.
The
foot switch (pedal) is used to
start a measurement cycle and to
operate the mixer off-line.
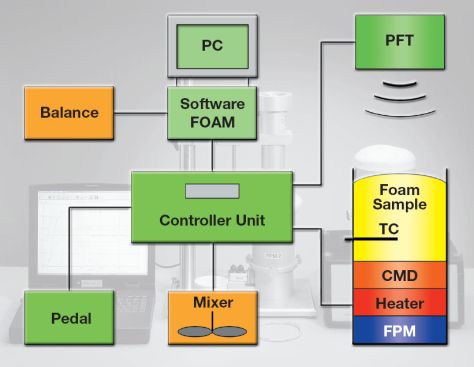
Fig. 10.
System survey of the Foam Qualification System FOAMAT and its
periphery.
top |