|
Schäume
testen
| Steighöhe und Steigprofil |
Reaktionstemperatur |
Steigdruck
|
Viskosität
|
Dielektrische Polarisation |
Temperatur geregeltes Probengefäß ATC |
Kistenschaum Messvorrichtung
|
Waage Integration
|
Systemzusammenstellung |
|
Schäume testen mit FOAMAT®
Messung physikalischer Größen bei der Entstehung von
Polyurethan-Schaumstoffen |
|
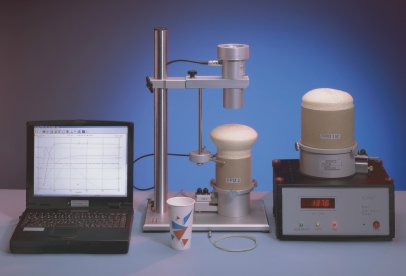
Bild 1. Das Schaumqualifizierungsystem FOAMAT mit Ultraschall
Gebläsesensor PFT, Thermolelement und den Druck-Messeinrichtungen FPM 2 und FPM
150. Die Benutzerführung, der Messablauf und die Datenverarbeitung werden vom
Programm SCHAUM (links) gesteuert.
* Durch mehrere Patente geschützt
|
Simultane Messung von Steighöhe,
Reaktionstemperatur, Steigdruck, Aushärtung, Gewichtsverlust und Viskosität
Erstellung von Masterkurven für
die Qualitätssicherung (ISO 9001)
Einfach bedienbare Windows
Software SCHAUM
Hochauflösende Sensoren für alle
Schaumtypen
|
|
Schäume
testen
Die Qualität von Polyurethan (PUR)-Schaumstoffen entscheidet sich bei ihrem
Entstehungsprozess. Es ist deshalb sinnvoll, die Entstehungsparameter durch
geeignete Messmethoden zu erfassen und regelmäßig an repräsentativen Proben zu
kontrollieren. Eine gleichbleibende Produktqualität wird dadurch gewährleistet,
dass mit Proben der Ausgangsstoffe vor dem eigentlichen Schäumungsprozess die
Entstehungsparameter gemessen und mit festgelegten Standards in Form von
Masterkurven verglichen werden. Dieses Verfahren wird von vielen
Automobil-Systemlieferanten für Teile des Fahrzeuginnenraums und für Anbauteile
angewendet. Auch in der Möbelindustrie und bei der Bau- und Geräteisolierung
werden die Entstehungsparameter zur Qualitätssicherung gemessen. Bei der
Entwicklung von Schaumstoffsystemen mit speziellen Eigenschaften bieten die
Entstehungsparameter einen Einblick in den Reaktionsverlauf bei der
Schaumbildung und wie dieser durch Additive, Treibmittel, Stabilisatoren und das
Mischungsverhältnis beeinflusst werden kann. Hier werden hohe Anforderungen an
das Schaumqualifizierungssystem FOAMAT (Bild 1) hinsichtlich seiner
Messgenauigkeit und der flexiblen Anpassung an verschiedene Probenformen
gestellt.
oben |
|
Steighöhe und Steigprofil
Das klassische Verfahren zur
Schaumstoffcharakterisierung ist die Steighöhen- oder
Steigprofil-Messung, bei der das Expansionsverhalten einer Schaumprobe
in einem Becher, einem Karton oder in einem zylindrischen Gefäß als
Höhenänderung erfasst wird. Aus der Höhenkurve werden mit Hilfe von
so genannten Kriterien die Startzeit und die Steigzeit ermittelt.
Obwohl diese Begriffe nicht genormt sind, ist die Startzeit nach
allgemeinem Verständnis der Reaktionsbeginn der gemischten
A(Polyol+Additive)- und B(Isocyanat)- Komponenten nach dem Ausbringen.
Die Steigzeit ist die Zeit bis zum Erreichen der maximalen Expansion.
Für die Messung der Steighöhe haben sich Ultraschall-Sensoren bewährt,
deren Genauigkeit durch die Einführung von
Ultraschall-Gebläse-Sensoren (Bild 2) noch erheblich verbessert wurde.
Sie besitzen integrierte Temperatursensoren für die
Schallgeschwindigkeits-Kompensation und sind für alle Arten von
Schaumstoffen, auch für Hartschäume mit hoher Wärmefreisetzung,
einsetzbar. Das Steigprofil ist der Fingerabdruck des Schaums, der in
der Qualitätssicherung mit vorgegebenen Master oder Referenzkurven
verglichen wird (Bild 3). Die Masterkurve stellt ein Toleranzband dar,
innerhalb dessen das Steigprofil einer „guten“ Schaumprobe liegen
soll. Derartige Masterkurven werden vom Qualitätsmanager aus einer
Schar von repräsentativen Steigprofilen erstellt. Sie stellen
Sollkurven dar, gegen die geprüft wird. Die Erstellung von
Masterkurven wird durch das Programm SCHAUM unterstützt und in
entsprechenden Masterdateien vollständig dokumentiert.
oben
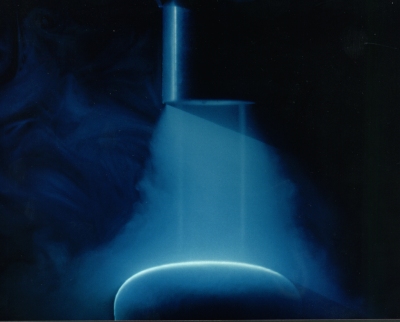
Bild 2.
Der patentierte Ultraschall-Gebläsesensor PFT ventiliert die
Oberfläche des expandierenden Schaums.
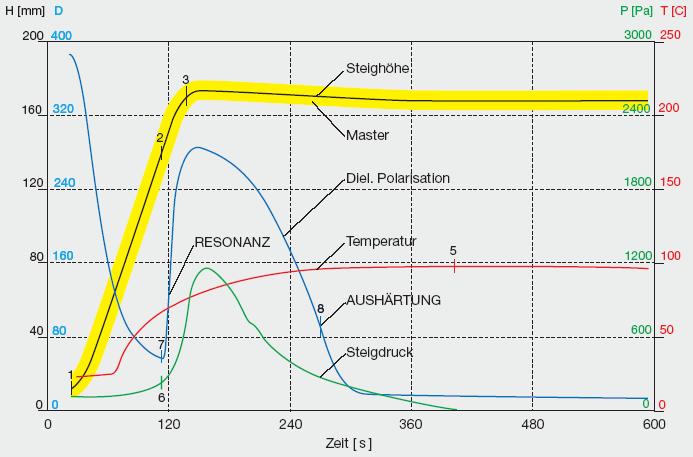
Bild 3: Die Messwerte für Steighöhe
(H), Dielektrische Polarisation (D), Steigdruck (P) und Temperatur
(T), werden vom Programm SCHAUM gleichzeitig aufgenommen und in einem
Diagramm dargestellt. Im Bild sind die Kurven für einen
Weichintegralschaum wiedergegeben.
oben |
|
Reaktionstemperatur
Der Temperaturanstieg in einer Schaumstoffprobe
wird durch die exotherme Vernetzungsreaktion erzeugt. Die
Schaumtemperatur ist jedoch keine homogene Größe, da sie von der
Wärmeabstrahlung an der Oberfläche des Schaumstoffes, der
Wärmeleitung durch die Gefäßwand, die Isolation durch den
Schaumstoff und die adiabatische Expansion beeinflusst wird. Der
Messaufpunkt ist damit entscheidend für den gemessenen
Temperaturverlauf. Wegen ihrer geringen Wärmekapazität und guten
Handlichkeit haben sich dünne Thermoelemente für die
Temperaturmessung im Schaum bewährt. Sie haben einen geringen
Einfluss auf die Schaumentstehung, stören nicht die übrigen
Messgrößen und lassen sich mehrfach verwenden. Um die maximale
Kerntemperatur zu erfassen, wird das Thermoelement im unteren
Drittel der Schaumstoffprobe eingesetzt.
oben |
|
Steigdruck
Druck entsteht im Schaum nach dem Abbinden der
Schaumkomponenten. Es bilden sich stabile Zellwände aus, die eine
weitere Expansion des Schaumstoffes und ein Entweichen der Treibgase
verhindern. So werden z.B. Wandelemente, Panele oder Bleche quer zur
Fließrichtung des Schaumstoffes belastet, wenn sie zur Isolation oder
Versteifung hinterschäumt werden. Die auftretenden Druckkräfte
erfordern Verstärkungen bzw. Abstützungen der
Produktionsvorrichtungen. Sie können im Extremfall zur Zerstörung
eines Bauteils führen. Diese Druckkräfte werden als Steigdruck
gemessen. Die Bezeichnung „Steigdruck“ wird deshalb gewählt, weil beim
abbindenden Schaumstoff lokale Spannungen vorhanden sind, die
wesentlich von der Steighöhe des Schaumstoffes beeinflusst werden. Zur
Messung des Steigdrucks wird ein spezielles Expansionsgefäß benutzt
(Bild 4), in das die reagierenden Schaumstoffkomponenten eingegossen
oder gespritzt werden. Der expandierende Schaum belastet den Boden des
Expansionsvolumens. Dort wird die Druckkraft gemessen. Das
Expansionsgefäß besteht aus einer Kartonhülse, die formschlüssig auf
ein zylindrisches Unterteil gesteckt wird, in dem sich ein Kraftsensor
befindet. Gegen Kontamination wird die Druckplatte durch eine PE-Folie
geschützt. Das Expansionsgefäß ersetzt den üblichen Testbecher.
Während die Steigkurve die Dynamik der Treibgasbildung wiedergibt,
spiegelt der Steigdruck die Zelleigenschaften wider, die durch die
Polymerisation beeinflusst werden. Bei der Entwicklung spezieller
Schaumstoff-Systeme, z.B. Polyester- Schaumstoffe mit sehr grober
Porenstruktur, kann die Druckmessung wichtige Informationen über die
Wirkung von Katalysatoren und Stabilisatoren auf die Abbindereaktion
bis hin zur Klebfreiheit und Nachreaktion (post-expansion) liefern.
Für die Produktion bestimmt der gemessene Druckverlauf die
Aushärtezeit des Schaumstoffes und legt damit den geeigneten Zeitpunkt
zum Öffnen der Form fest. Ein Reißen des Schaumstoffes, eine
Nachreaktion oder eine zu lange Verweilzeit in der Form können dadurch
vermieden werden. Da der Schaumstoff auch während der Druckmessung
nach oben frei ist, kann zeitgleich die Steighöhe mit dem
Ultraschall-Gebläsesensor gemessen werden.
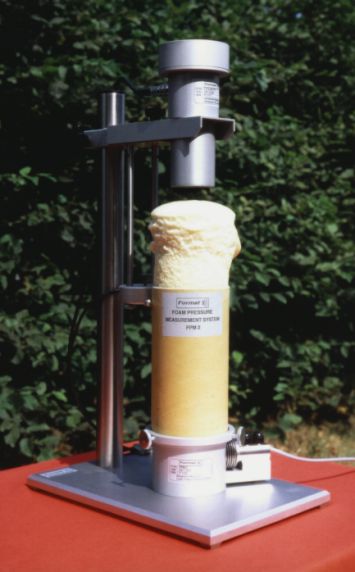
Bild 4. FPM 2 auf dem Stativ
des Schaumqualifizierungssystems FOAMAT®.
|
|
Viskosität
Ein besonderer Vorteil der Druckmessung am Boden
eines zylindrischen Expansionsgefäßes besteht darin, dass aufgrund der
speziellen Geometrie der Messanordnung die Viskosität des entstehenden
Schaumstoffes kontinuierlich aus den Messdaten berechnet werden kann.
Eine direkte Viskositätsmessung mit klassischen Rotations- oder
Vibrations- Viskosimetern ist für Schäume wegen ihrer Volumenzunahme
und dem Übergang in die feste Phase experimentell schwierig und somit
für Prozessparameter ohne Aussage. Der Prüfkörper taucht
unterschiedlich tief in den Schaum ein, sitzt am Ende im Schaumstoff
fest oder gräbt sich seinen Weg frei, d.h. er verliert die Kopplung an
den Schaum. Diese messtechnischen Probleme werden durch Anwendung des
Viskositätsmodells von Hagen-Poisseuilles umgangen. Das
Modell geht davon aus, dass die Viskosität durch die Kraft bestimmt
wird, die benötigt wird, um ein Längenelement einer Schaumprobe mit
einer bestimmten Geschwindigkeit durch ein Rohr, hier Papphülse, zu
bewegen. Natürlich wird der Schaumstoff nicht von außen durch die
Papphülse gepresst, er macht das selbsttätig indem er expandiert. Von
außen wird nur die Reaktionskraft gemessen, die sich direkt aus dem
Steigdruck ergibt. Die Druckmessung und die Steigkurve in einem
zylindrischen Expansionsgefäß liefern damit alle Daten, um die
Viskosität lückenlos zu berechnen.
oben |
|
Dielektrische Polarisation
Die Dielektrische Polarisation ermöglicht,
unabhängig von den mechanischen Parametern, einen Einblick in die
elektro-chemischen Abläufe bei der Schaumstoffbildung. Die flüssigen
Ausgangsstoffe leisten mit ihren polaren Molekülen einen hohen Beitrag
zur Dielektrischen Polarisation. Während der Kettenbildung und der
anschließenden Vernetzung nimmt die Dielektrische Polarisation
kontinuierlich ab. Sie erreicht nach dem Aushärten einen konstanten
Wert. Das Polarisations-Signal wird, außer von den molekularen
Dipolmomenten, auch von der abnehmenden Dichte während der Expansion
des Schaumstoffes beeinflusst. Falls in der Steigphase von
Weichschäumen trotz- dem eine Zunahme der Dielektrischen Polarisation
beobachtet wird, so leistet der als Zwischenprodukt gebildete
Polyharnstoff einen überproportionalen Signal- Beitrag (Resonanz).
Reproduzierbare Messung der Dielektrischen Polarisation setzen voraus,
dass ein Formschluss zwischen dem Schaumstoff und dem
Polarisations-Sensor CMD (Curing Monitor Device) vorhanden ist. Dieses
wird durch die Anordnung des Polarisations-Sensors am Boden des
Expansionsgefäßes sichergestellt (Bild 5). Der Schaumstoff wird dort
flächig durch den Steigdruck (s.o.) angepresst. Für produktionsnahe
Testbedingungen kann der CMD-Sensor mit einer geregelten Heizung
ausgestattet werden. Die Dielektrische Polarisation wird als
elektrische Kapazitätsänderung durch den Schaum, bezogen auf das
leere Expansionsvolumen, gemessen. Aus ihrem Verlauf lässt sich die
Abbindezeit und die Aushärtung, insbesondere von Weichschaumstoffen,
bestimmen. Ein weiterer Aspekt sind Aussagen über katalytische
Wirkungen, z. B. von Aminoverbindungen, und die
Reaktivitätsklassifizierung.
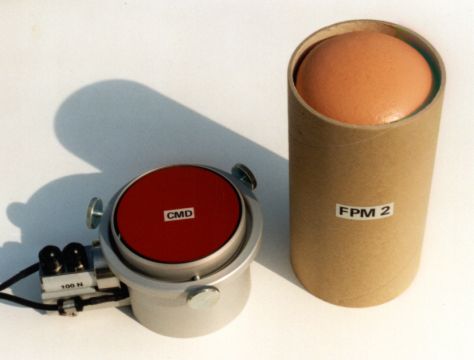
Bild 5.
Mit dem Polarisations-Sensor CMD wird die
Dielektrische Polarisation einer Schaumprobe zeitgleich mit dem
Steigdruck gemessen. Rechts die Schaumprobe in der abgenommenen
Kartonhülse.
oben |
Temperatur geregeltes
Probengefäß ATC
Undefinierte Probengefäßtemperaturen beeinflussen die Übertragbarkeit
der Messergebnisse auf die Produktionssituation. PIR Schäume benötigen
zum Reagieren und Aushärten eine externe Wärmezufuhr. Anderenfalls
bleiben diese Schäume klebrig und bilden Lunker. Hiervon ausgehend hat
Format Messtechnik GmbH das Temperatur geregelte Probengefäß ATC
(Bild 6)
entwickelt. Ein weiterer Vorteil des ATC ist die bessere
Reproduzierbarkeit der Messungen im Vergleich zu nicht Temperatur
geregelten Probengefäßen.
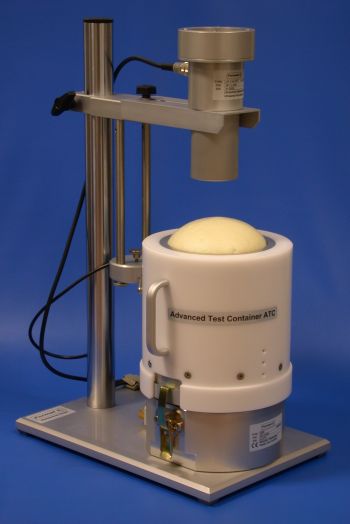
Bild 6.
Das temperaturgeregelte
Probengefäß ATC liefert reproduzierbare und produktionsnahe
Versuchsergebnisse.
oben |
Extra großes
temperaturgeregeltes Probengefäß ATC XL
Um größere
Ansätze unter definierten Probengefäßtemperaturen zu prüfen, hat
Format Messtechnik GmbH das extra große temperaturgeregelte
Probengefäß ATC XL (Bild 7) entwickelt. Der ATC XL verfügt über
ein vierfach größeres Probenvolumen als der Standard ATC. Beide
verfügen über ein Ober- und ein Unterteil, welche über Schnappverschlüsse
miteinander verbunden werden. Die Schaumprobe kann einfach über die
Öffnung im Boden des ATC XL Oberteils entfernt werden. Zudem ist ein
Ausdrückwerkzeug vorhanden.
Bild 7.
Der ATC XL ist auf
dem Stativ des Schaumqualifizierungssystems FOAMAT®
platziert. Der ATC XL verfügt über ein vierfaches Prüfvolumen im
Vergleich zum Standard ATC.
oben |
Kistenschaum
Messvorrichtung
Die Kistenschaum Messvorrichtung umfasst den Box
Foam Container BFC 200, das vergrößerte Messstativ und
das metallgemantelte Thermoelement. Die Kistenschaum Messvorrichtung
wurde speziell für die Erfassung der Steighöhe und der Kerntemperatur
von Blockschaumformulierungen entwickelt. Der BFC 200 besteht aus
Pertinax Wänden, mit einer Inneren Kantenlänge von 200mm. Für eine
einfache Probenentnahme sind zwei Seitenteile mit Scharnieren
versehen, so dass sie zur Seite geklappt werden können. Am oberen Rand
des BFC 200 ist ein Thermoelementhalter befestigt. Er dient dazu, das
Thermoelement im Zentrum der Schaumprobe zu platzieren. Das
vergrößerte Messstativ ist größer als die Standardausführung und ist
mit einem zweiten Becherhalter ausgestattet, der auf die rechte Seite
des Stativs geschwenkt wird.
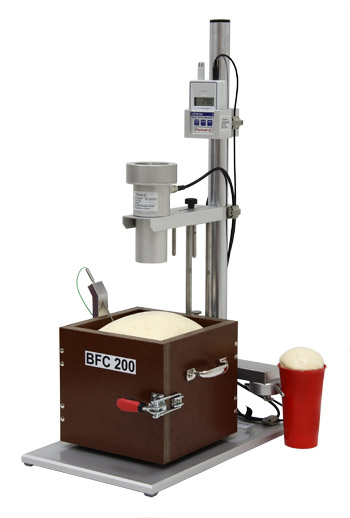
Bild 8.
Der BFC 200 ist auf der
Grundplatte
des vergrößerte Messstativs platziert. Das Thermoelement ist im
Zentrum des Schaums positioniert.
oben |
Waage
Integration
Beim Messen von Steigprofilen und anderer physikalischer
Größen ist die exakte Einwaage der Reaktionskomponenten die Voraussetzung für
reproduzierbare Messergebnisse. Die Integration einer Laborwaage (Bild 9) in den
Messablauf bietet die Möglichkeit, die Massen der einzelnen Komponenten beim
Einwiegen automatisch in ein Ansatz-Protokoll zu übernehmen. Zusätzlich kann der
Masseverlust infolge der Freisetzung von Treibgasen und leicht flüchtiger
Komponenten während des Aufschäumens kontinuierlich gemessen werden. Die
automatische Bestimmung der Rohdichte aus der Masse der fertigen
Schaumstoffprobe und der gemessenen Endhöhen ist ein weiterer Nutzen einer
integrierten Waage. Für die simultane Steighöhenmessung wird der Probenbecher
auf die Waage gestellt. Alle Massedaten werden gespeichert und in einem
Prüfprotokoll zusammen mit den übrigen Messkurven ausgegeben.
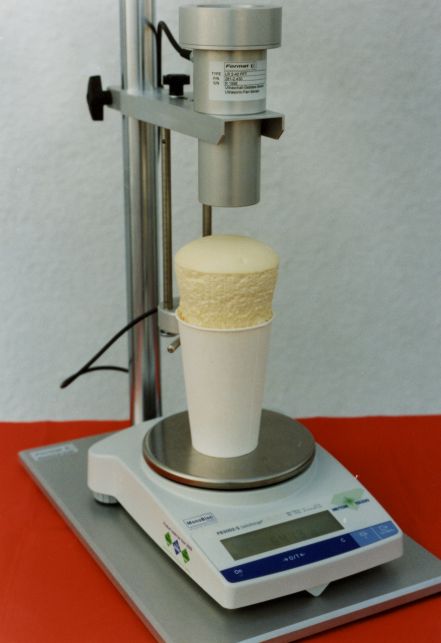
Bild 9.
Zur Bestimmung des Masseverlustes wird der
Probenbecher auf einer Laborwaage mit serieller Schnittstelle positioniert.
oben |
|
Systemzusammenstellung
Das komplette Schaumqualifizierungssystem FOAMAT
und die angeschlossene Peripherie sind in Bild 8 schematisch
abgebildet. Der Rührer wird vom Programm SCHAUM entsprechend den
Benutzereingaben, gesteuert. Für 3-phasige Drehstromrührer sind
spezielle Adapter erhältlich. Das Steuergerät und die Waage sind
über je eine serielle Schnittstelle mit dem PC verbunden. Der
Fußschalter dient zum Starten der Messung und zur Mixeransteuerung.
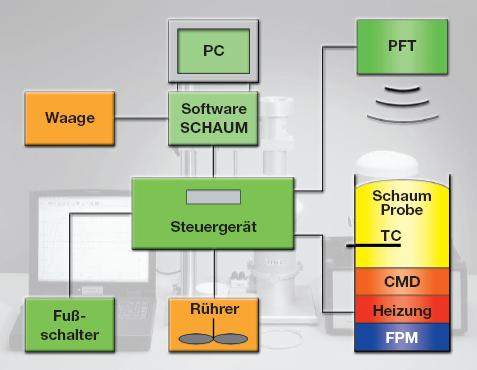
Bild
10. Systemübersicht des
Schaumqualifizierungssystems FOAMAT und der angeschlossenen
Peripherie.
oben |
|